As with any rapid rise in adoption of new technology, like the automated storage and retrieval systems (ASRS) of today’s complex automated warehouses, there are increased risks. Fire is the most severe of them all. Not only is there a huge loss of goods in a warehouse blaze, there are also serious implications for the local community and business. These include potential loss of life, evacuation of neighbouring properties, business continuity, smoke and environmental pollution and crash in consumer confidence.
Why does an ASRS increase the risk of fire?
UK grocery retailer Ocado experienced two consecutive fires in their automated warehouse in Andover, England. The first fire resulted in complete destruction of the site and the second fire cost £35 million in lost revenue.
Investigations revealed that these fires were caused by malfunctioning robots which either collided with storage racks or each other. Reports also suggest that, in the second fire, the sprinkler system activated but wasn’t sufficient to put out the fire due to the high density of the storage which was alight.
Additional causes of fire in an ASRS include:
- plastic bins that are stacked closely together, reaching high and wide
- cables that, when damaged, expose live wires.
Is an ASRS worth the increased fire risk?
An ASRS speeds up the ‘receive, put away, store, pick, pack and ship’ process in a warehouse. Through robotics, software and racking solutions, they strive to meet the growth of ecommerce and ever-increasing demands of consumers.
An ASRS enables greater storage density, increased efficiency and faster turnaround of goods, ticking all the boxes for a manufacturer, retailer, distributor and, most importantly, consumer.
As commodities are able to be more tightly packed into a smaller space, the need for a fire protection strategy becomes essential. There are more goods, more packaging and more flammable materials squeezed into a restricted area.
How do I prevent a fire in my complex automated warehouse?
It’s critical to integrate an appropriate fire protection solution into the planning of your ASRS. This should include automatic fire sprinklers and the consideration of fire brigade intervention and manual fire fighting efforts.
Before a fire protection specialist can advise on solutions, they’ll need to have a good understanding of the type of goods you store and the workflow of your warehouse to fully understand your set up and the ASRS you’ve chosen.
What type of goods are you storing?
The type of goods a warehouse stores influences the design of automatic fire sprinkler systems. Typically, commodities, and their packaging, can be categorised into the following:
Category 1: goods of non-combustibility or relatively low combustibility
This includes products like electrical appliances (low plastic content), metal goods, glass, non-combustible liquids, meat and food products.
Categories 2 to 4: combustible goods
This includes paper, food products and products with expanded (foamed) plastics less than 25% by volume or unexpanded plastics and polyurethane less than 15% by weight.
Category 5: goods containing unexpanded plastics greater than 15% by weight
Packaging must not include expanded plastics greater than 40% by volume or 10% by volume where the expanded plastic surrounds the commodity.
Category 6: expanded plastics
This includes plastics such as styrene, foam mattresses and polyurethane.
Additional categories:
Special commodities: products by their nature requiring additional consideration, which includes combustible and flammable liquids, aerosols, alcohol, tyres, carpet and hanging garments.
Dangerous goods require further consideration and typically the involvement of a specialist dangerous goods consultant.
What does your workflow look like?
Workflow influences fire risk in a warehouse. It’s important your fire protection specialist understands when and how goods are stored, loading and staging areas and where consideration is required for the separation or segregation of goods that shouldn’t be stored together.
A well-designed fire protection system will provide warehouse operations maximum flexibility and mitigate risk.
Have you chosen the right ASRS for your complex automated warehouse?
Your specialist ASRS provider works closely with you, and your fire protection team, to scope out the best system for your business. The most common types of ASRS include:
Rack structure ASRS
These are used for pallet storage and loaded by crane or vertical lifting systems into the racking structure.
Mini-load ASRS
These are used with individual cartons or items of storage, placed onto trays, containers or totes and loaded into multi-level storage systems by automated processes.
Top-loading ASRS
These are open-top 5-sided containers for storage of goods, which are loaded and unloaded vertically into a dense storage array by automated robotic systems.
Enclosed ASRS
These are typically used for high-value parts storage which are susceptible to heat, water or smoke damage. They’re vertically enclosed systems and typically lift or carousel. Lift systems use robotic pickers to deliver or remove stored items from the storage support system. Carousel systems use rotating storage arrangements to deliver the storage tray to warehouse staff.
Choosing an ASRS with low fire risk
Pallet-style systems are considered a lower fire risk than top-loading or mini-load ASRS systems. This is why:
Vertical storage
Mini-load or pallet-style systems use a horizontal storage space which means that goods are compact and organized with a reduced storage density. This allows for installation of in-rack sprinklers. In contrast, top-loading ASRS systems typically use vertical storage and stack goods on top of each other which increases storage density and fuel load. This typically doesn’t allow for the installation of in-rack sprinklers.
Separation of stored goods
In a mini-load or pallet-style ASRS system, stored goods are typically separated by flues. This separation allows prompt heat venting of storage and means that sprinklers can operate quickly. This reduces horizontal fire spread and allows the penetration of water through the storage structure from the operating sprinkler system. In contrast, top-loading ASRS systems typically have no separation between the goods, which means that the fire can spread quickly and easily.
ASRS fire protection solutions
No 2 fire protection solutions are the same. Even if a large online retailer has identical warehouses that store the same goods in Sydney and London, each country will have different regulatory, authority and fire brigade requirements.
These are the 3 main pillars of a fire suppression strategy.
Fire sprinkler systems
Each type of ASRS requires a different automatic fire sprinkler system design which includes the integration of fire sprinklers into the storage structure. The fire protection team collaborate closely with the automation system provider to establish criteria for integration, including location of fire sprinkler pipework, location of sprinkler heads and use of horizontal and vertical barriers.
For these to be effective, as illustrated by the Ocado disaster, commodity storage and associated sprinkler systems need to be compliant with appropriate fire codes.
Fire brigade intervention
It’s important to include consultation with the fire brigade authority that has jurisdiction of the ASRS facility throughout the design process. ASRS facilities present unique challenges to the attending fire brigade, largely due to the density of storage, storage of dangerous goods and special commodities and the potential for extended duration fires.
Through consultation, you can agree on the:
- firefighting water supply
- firefighting approach, particularly within the ASRS structures
- design of fire protection systems to support and facilitate safe fire brigade intervention.
Manual fire fighting
Australian standard AS 2419.1:2021 excludes ASRS warehouses from its scope but it does provide guidance on fire protection measures.
This includes an access and egress system which is designed to facilitate the safe movement of firefighters in and out of building and storage array during firefighting and emergency response. This system includes requirements for the size and location of access points as well as provisions for safe entry and exit procedures.
The updated standard also includes new requirements for smoke hazard management with a focus on ensuring that smoke can be effectively cleared from buildings to improve visibility and reduce the risk of firefighter injury. This includes provisions for smoke detection and ventilation systems and requirements for smoke management plans and procedures.
It’s not enough to focus on the technology
Every complex automated warehouse that has an ASRS with a robust fire protection strategy will be aware that proper maintenance, regular inspections and adherence to fire safety codes and standards are essential for their systems to remain safe and reliable. Without these, they’re in serious danger, both of fire and significant business penalties.
Our fire protection team has a deep understanding of local and international fire protection standards and codes and how these apply to some of the largest and most complex automated warehouse systems globally.
We build flexilibity, efficiency and value for money into the solutions we advise with each solution is specifically engineered and tailored for the risk and business needs.
For a complex automated warehouse, it’s about a storage system that has the right products in the right places and just the right amount of breathing space to stay safe. It’s about protecting your people and your goods and staying compliant. It’s about smart systems that meet your business’s needs today and are future-proofed for tomorrow.
Listen to Jeremy’s summary of this Insight
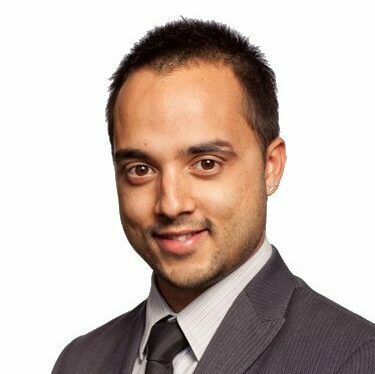
Meet our Group Technical Director – Fire Protection Services, Jeremy Donohoe
“My father was a domestic builder and I recall he would always point out the various houses he had built as we drove past them and I would spend many school holidays as a child on building sites assisting him. I got an appreciation of the building trade and the satisfaction of seeing projects come out of the ground and reaching completion.
“Studying engineering, and then establishing a career in building services engineering, was just a natural progression.”