As the specialist high-rise structural consultant, our design has been a critical part of gaining planning approval. This has finally been achieved after almost 3 years in development.
According to the World Green Building Council, buildings are currently responsible for 39 per cent of global energy related carbon emissions: 28 per cent from operational emissions and 11 per cent from materials and construction.[1]
The 11 per cent associated with materials and construction, also termed embodied carbon, is becoming increasingly critical to address. This will soon become the lion’s share of the built environment’s carbon emissions as energy grids decarbonise in the lead up to our global 2050 net zero emissions target.
James Dibble, Managing Director, Grange Development, says “We believe that hybrid buildings are the future of our built environment. Those ambitions must also be balanced with the reality of the cost implications.”
He continues, “We can’t grow concrete. C6 is a big deal because it provides a commercially viable and practical template that reduces CO2 emissions and encourages us to take responsibility for our part as a major contributor.”
Ambitious design
We worked closely with architects, Fraser & Partners, to make the structure work and to create a template for future projects. Their philosophy for the design was to build with ‘economy, efficiency, discipline and order’ so the building would minimise the quantity of materials used and prioritise responsible material procurement by using Australian sourced mass timber.
By fine tuning the design, we were able reduce the cost and extent of the building’s structural elements from the initial structural concepts. An integral part of this was achieving a column grid that maximised valuable spaces while balancing the need to avoid deep timber beams. This allowed the architect to achieve larger apartments and communal spaces and added financial and social value to the building.
We also introduced outrigger walls, minimised the thickness of the concrete core and eliminated a number of concrete shear walls and steel bracing elements that had been proposed prior to our involvement, all in an effort to save cost and carbon.
Integrated thinking
During the schematic design stage, the timber structure required coordination with both the architect and fire engineer. However, as the design progressed, the timber floor structure required the most coordination of any structural element, needing input from architects, specialist mass timber consultants, services engineers, fire engineers and acoustic engineers. This coordinated thinking will be crucial to the construction of the project.
Structural Challenges in a tall slender building
Designing a tall, slender building comes with many challenges:
Wind
Tall buildings are more susceptible to wind forces so managing loads is crucial. We needed to consider the building’s shape, orientation and local weather patterns to ensure stability, safety and comfort.
We worked closely with the wind engineer to ensure accurate wind loadings were applied which meant that strength and sway criteria met Australian standards.
Foundations
These need to support the building when it’s impacted by wind. The foundations nearest to the side of the wind should stay firm while resisting lateral forces and distributing the building’s weight evenly. Soil conditions play a significant role in achieving this.
Weight
In high-rise structures, the weight of the structure can cause concrete shrinkage where each column shortens marginally. In shorter structures this is insignificant, but when over 40 levels the accumulated shortening can cause issues, especially for facades.
Gravity
The higher you go, the greater the chance of the structure buckling or collapsing.
Materials
Choosing the right materials balances strength, flexibility and durability and ensures the structure can withstand the forces acting on it.
The structural detail of the C6 tower
Our brief was to design a structural system that provides stability, strength and support over 54 storeys.
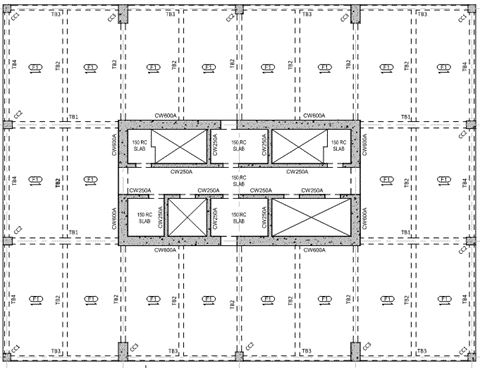
Typical floor – structural framing (plan view)
Materials
In Australia, high-rise structures are typically made from concrete. The construction materials for C6 are made up of approximately 40 per cent timber, by volume. The design uses around 42 per cent less concrete than a traditional building of a similar scale.
We’ve been able to use timber for parts of the structure where it will either outperform or equal the performance of steel and concrete. This is assessed on both a strength to weight ratio and performance over a building’s lifetime.
By combining steel, concrete and timber into the structure, we’ve been able to design for optimal performance and create a hybrid structure.
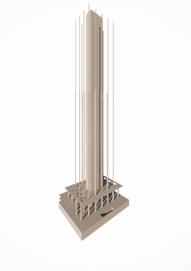
The concrete
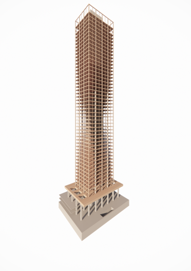
The timber
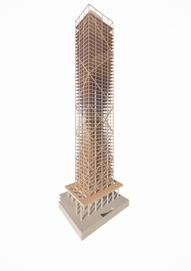
The steel
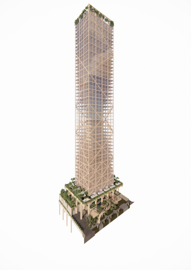
The whole package
Timber supply
The lead time for timber is still relatively long. This means that the timber floors must be fully designed and coordinated early. The long lead time also has a flow on effect for the concrete design as the timber connections need to be finalised before a timber order can be placed and production begins.
Penetrations in the floor plate and beams also need to be locked in as changing sizes and locations of penetrations after timber production has started can lead to significant delay and additional costs.
Prefabrication
Other than the foundations and in-situ concrete core system, structural members are typically prefabricated off-site.
Foundations and retention
The team are still in the process of designing the foundations for C6. There are two likely solutions being investigated. Both consist of piles founded within the cemented sand layer that’s approximately 34 metres below the surface.
The most likely outcome is a conventional pile-only solution, however, we’re working with the project’s geotechnical engineer to also look at the feasibility and cost-effectiveness of a piled raft solution.
Piled foundations are often used to transfer significant hydrostatic, wind and earthquake forces through shallow soil profiles to a more competent material. In South Perth, much of the shallow soil profile is medium-dense silty sand which is an insufficient founding material for a tall slender tower.
A range of pile foundation options are currently being assessed on C6, including Continuous Flight Auger (CFA), Bored Piles and Barrette Piles.
Being in South Perth, so close to the Swan River, a D-wall (diaphragm wall) has been adopted as the most robust retention system, to provide a watertight perimeter to the basement of the development.
Weight
By using timber for a large part of the structure, we’ve been able to minimise the building weight and reduce foundation sizes and concrete volumes when designing for gravity loads. However, reducing the weight of a building this tall is a double-edged sword.
The unique challenge for C6 is the lightness of the building relative to its height, which, when subjected to wind loads, poses the risk of the windward foundations being pulled out of the ground. This will be a key area of focus for us as we progress the foundation design.
Concrete shrinkage
We’ve designed the columns as pre-cast to help manage the total concrete shrinkage component onsite and in doing so control axial shortening of the columns, by allowing the early age shrinkage to occur before installation. Differential axial shortening between adjacent vertical elements is a significant consideration when designing high-rise structures, so considering this early in the design is key to having confidence around the concrete column sizes.
Core
The core of a building, as its name indicates, is the fundamental stability system of the building’s structure. It’s often designed to be the only thing holding a building up in an earthquake or powerful gust of wind.
For C6, as in most high-rise structures, the core structure is the elevator and stair shaft, and due to the height of the building, concrete is the most feasible option to provide the strength and stiffness required.
Outrigger walls
One of the key features of this core system is the outrigger walls which allow us to minimise the concrete volume in the core. These walls, placed on chosen levels, span between the core and specific perimeter columns to aid the core in resisting lateral loads. These walls work in the same way as their nautical namesake, letting the core of the building ‘lean’ on perimeter supports to help avoid overturning.
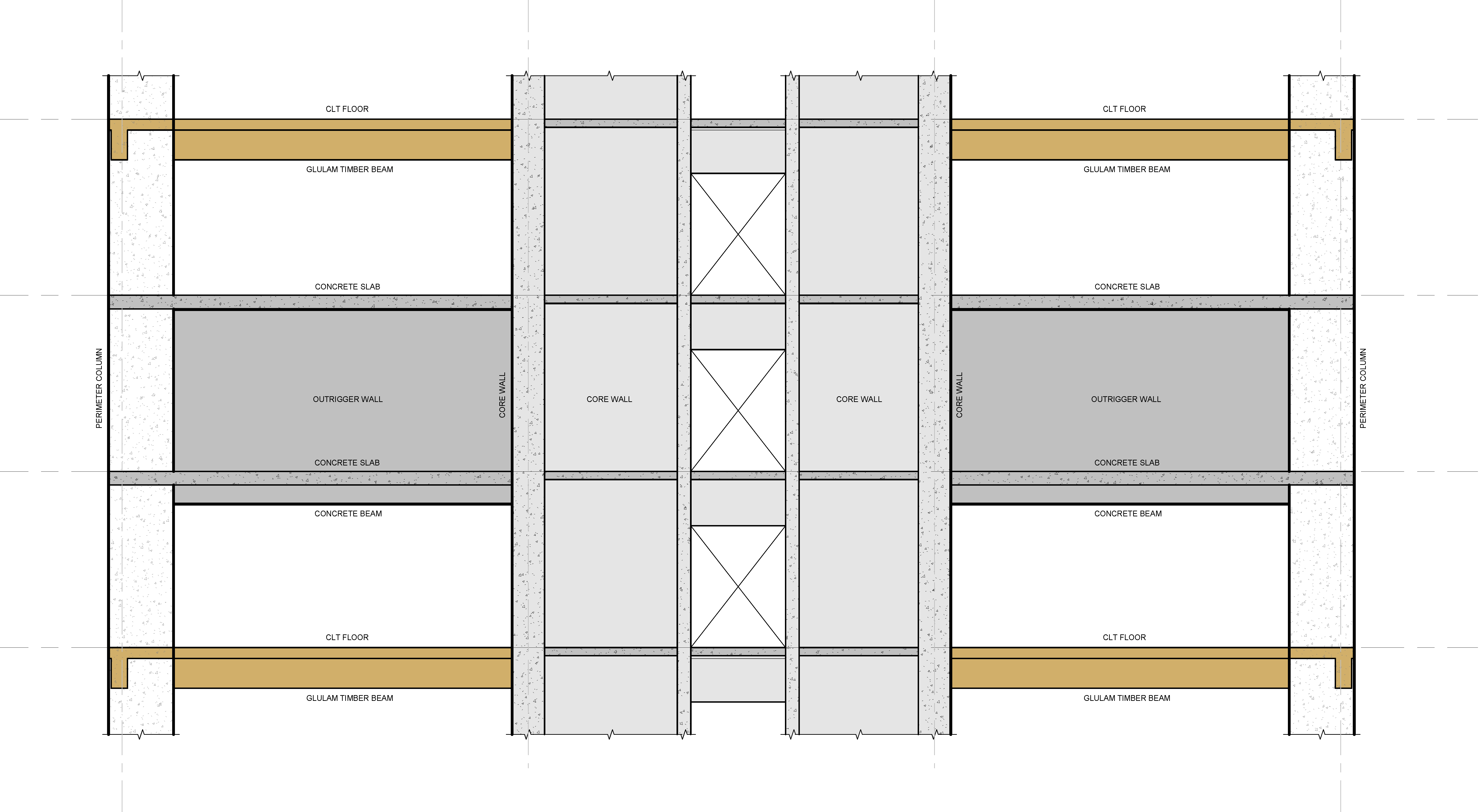
Outrigger system (elevation view)
Columns, beams and slabs
Columns
We’ve designed the concrete columns as double-height pre-cast columns to take full advantage of the speed of construction of timber floors. In a building this tall, timber columns aren’t feasible due to the enormous, accumulated load on the columns as you travel down the building as well as the stringent fire requirements on these integral primary load bearing elements.
We’re still able to keep embodied carbon as low as possible, however, by opting for double-height pre-fabricated columns that minimise concrete waste and transport. By maximising construction speed, we allow more time for design coordination before the timber production deadline.
Designing the vertical members as concrete both enables great heights and helps solve fire engineering issues that often stop a project of this kind from ever reaching design development.
Slabs & Beams (floors and roof)
In high-rise structures, most of the concrete volume is within the floor system. Designing the floors as timber minimises the volume of concrete we use significantly.
Residential buildings typically have relatively low in-service loading, so timber joists, bearers and flooring are a very common solution. On these typical residential levels, the team has opted for timber beams to carry a series of cross laminated timber (CLT) panels to distribute the load from the floors to the perimeter columns.
On other ‘non-typical’ levels, such as the podium levels, mid-rise plant levels and roof, we’ve opted for an efficient post-tensioned concrete structure for various reasons including durability, heavy loading and contribution to the stability system.
The first 6 floors in the tower are communal ‘podium’ floors.
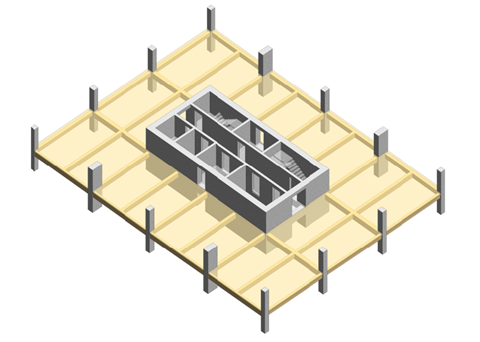
Typical floor – structural framing (3D view)
Podium
The 6 podium levels (including 2 basement) are retained as concrete due to a number of feasibility items:
- Durability: the podium levels incorporate car parks and other areas of high wear and tear. They’re also exposed directly to the weather in areas. Timber wouldn’t be the most practical solution.
- Transitions of concrete column sizes and shapes: these are very difficult to achieve with a timber floor plate.
- Areas of high loading: such as deep planting zones, where timber wouldn’t have the strength or stiffness of concrete.
The cost of a timber building
At first glance, a timber building may appear significantly more expensive than a traditional building. However, this can be a short-sighted view as it often doesn’t take into consideration the entire lifecycle of the building, estimated at 50 years.
- Prefabricated timber is quicker to build than steel or concrete, reducing the construction time of a project. Given that over 40 of the floors are constructed of mass timber, we expect this will save over 100 days in construction time.[2]
- Fabricating the structure in parts off-site, for example the double-height precast columns, enables construction of multiple parts of the building at the same time, further expediting the build. It also reduces material wastage and is a far more sustainable approach.
- Timber has become more desirable than steel or concrete and attracts a higher premium from tenants and buyers. It’s recognised for its sustainability attributes not only as a lower carbon material, but also because:
What’s next for the structure of C6?
We haven’t solved all the challenges – the project is still in advanced design development stage. Our next steps include:
- working with the geotechnical engineers to design the foundations of the building, carefully considering the potential for uplift
- developing the design of the vertical elements to achieve optimal member sizes
- working with the floor designers, Vistek, to coordinate connections between the floors and vertical elements
- working with the architect, Fraser & Partners, to resolve any clashes between architectural and structural requirements prior to construction.
Our predictions for the future of MASS timber buildings
As mass timber comes to the forefront of minds and design, we expect to see more hybrid structures combining the strengths of concrete, steel and timber. In particular, we see potential for buildings that have simple floor geometries with plenty of party walls for the vertical structure. These include residential developments, hotels and aged care as the ‘sweet spot’ for the adoption of mass timber and hybrid structures.
Current hurdles are based on a fear of the unknown and the more exposure that developers, building surveyors and builders have to mass timber, the smoother and easier the process becomes.
We believe the growth in hybrid timber construction will accelerate as the new-build market picks up. This will demand an increase in supply, locally and internationally.
NDY is currently designing the structure on a series of other projects that incorporate mass timber. These include an industrial warehouse and commercial office building in Melbourne.
Our building services team has similar experience, recently completing projects such as the Boola Katitjin Building in Perth, Australia and the Wurriki Nyal Civic Precinct in Geelong, Australia.
Once C6 has been completed, Grange Developments has committed to openly publish the system-based design approach. This will allow a tried-and-tested hybrid construction methodology to be easily adapted across multiple building typologies, heights and locations so it can become the new industry standard.
[1] https://worldgbc.org/advancing-net-zero/embodied-carbon/
[2] A typical concrete floor can take 5 to 10 days to build. Floor construction using the mass-timber members can range from 4 hours to 1 day.
[3] Addressing Embodied Energy With Mass Timber | Passive House Accelerator
[4] The Biophilic Response to Wood: Can it Promote the Wellbeing of Building Occupants? | ArchDaily
Footnote:
The design to-date has involved a collaboration between Grange Development, Fraser & Partners, REALMstudios, Vistek structural engineers, TMBRConsult, Slattery and Holmes Fire.