Our electrical consultants were recently able to identify the source of a power outage on a large project through effective meter monitoring that we’d installed 12 months before.
Our client called us in to investigate why their power had failed and we were quickly able to see the downtime correlated with a dip in mains voltage. Further analysis identified that the dip in voltage also married up with a dip in frequency which resulted in an equipment fault.
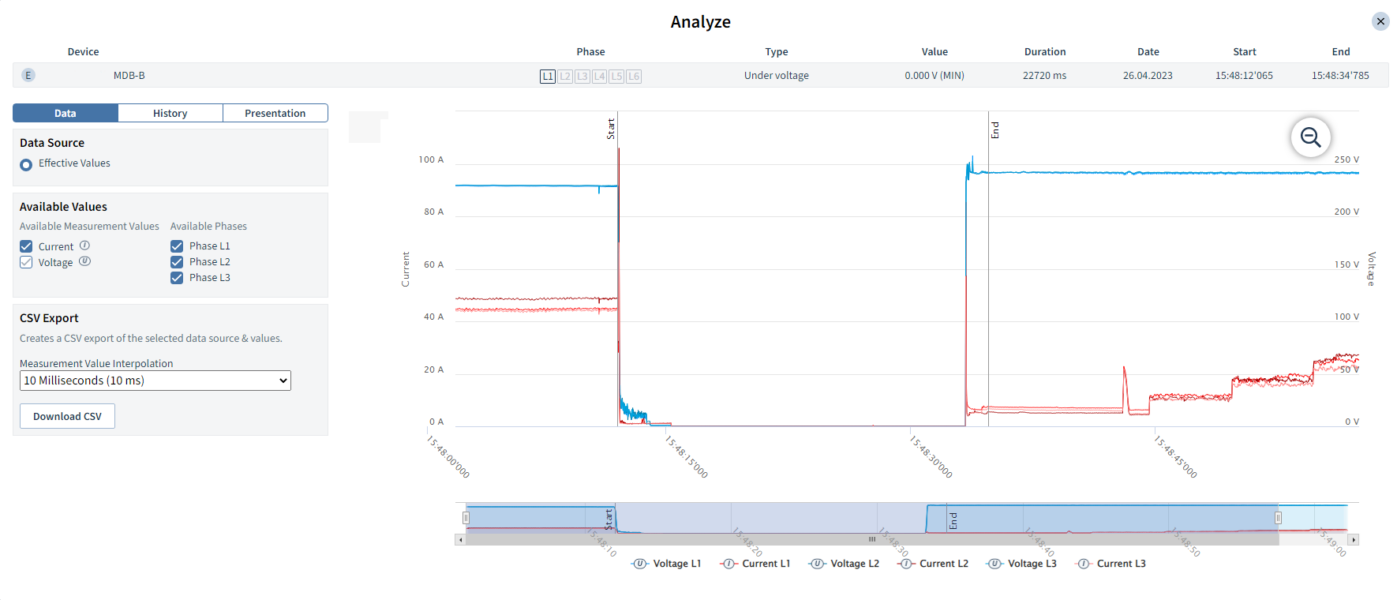
Can your meter capture this detail? The meters we installed were able to capture the moments preceding and following the outage.
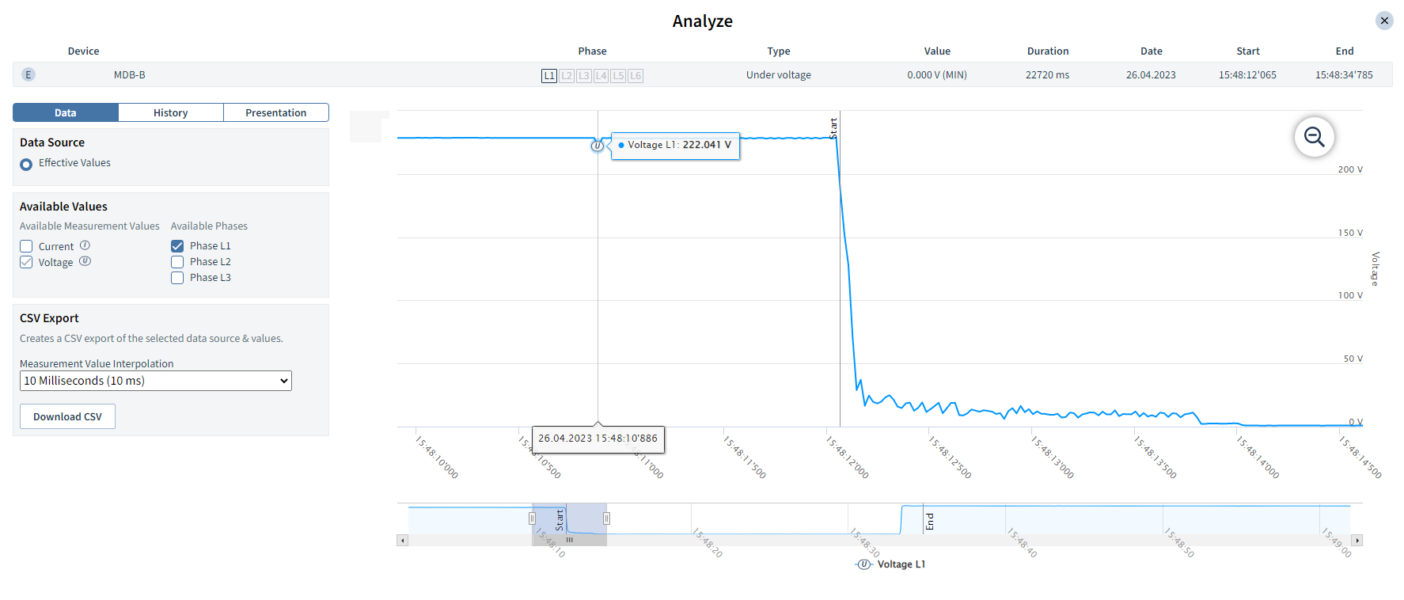
Don’t miss the little things. The cause of this fault was not the outage but instead this little dip in voltage which correlated with a frequency dip.
We were then able to review voltage and frequency both upstream and downstream of their uninterruptable power supply (UPS), revealing a weakness in the configuration. Our solution was to reconfigure the UPS from eco to full double conversion mode so it could sustain power during variation in mains power frequency in the future.
This easy analysis, including development of a solution, took a few hours and was only possible because we could quickly identify the exact timing of events throughout the fault and align them with when the equipment fell over. Actioning the solution onsite took another few hours.
As this fault had the potential to impact a construction project made up of multiple sequential sites and a restrictive time program, operational continuity was critical. Without effective meter monitoring, this analysis and solution wouldn’t have been possible. Investigations would likely have taken several months during which the project would have been paused.
What can a meter do?
Electrical meters have moved on from only summing up energy use. Most meters these days support hundreds of measuring parameters and can store and communicate large quantities of data.
Electrical meters monitor the quality of electrical power in a building – something we can’t see. Their ability lies in how we set them up, including integration across multiple business systems, and how we analyse the power quality issues they identify. When done well, they can help to highlight which equipment is performing poorly and improve reliability and energy efficiency.
Depending on a meter’s sophistication, its key functions include monitoring harmonics, voltage, currents and the power and frequency of an electrical supply. More advanced devices can spot transients, sustained power quality events and capture waveforms when thresholds are exceeded. When connected as part of a complete system, a meter can also collect and store data over a period of time and generate reports.
Power quality meters play a crucial role in diagnosing power disturbances and identifying the root causes of the problems that jeopardise power.
Reduce risk
Many critical businesses install power quality meters after a period of unforeseen and damaging downtime with the aim of preventing an outage happening again. Their goal is to minimise risk to a site, through proactive monitoring of power.
Identify early signs of equipment failure
Meters can identify system interruptions (trips), sags, swells, voltage fluctuations, harmonic disturbance, power overload and equipment load changes over time, among other things.
Monitoring, and subsequent analysis, allows an electrical team to identify the source of the compromised power quality. By understanding what happened, an electrical specialist can work out how to fix it and prevent it happening again. These fixes are known as power quality correction solutions.
Solutions can include replacing ageing equipment, sorting out loose connections, installation of harmonic correction or surge protection devices.
Code compliance
Businesses are required to meet local obligations in line with their electrical distribution code and distributor supply agreement. Meters can highlight factors which show where compliance isn’t being met, including both customer and distributor obligations:
- Customers are obligated to maintain current harmonics and power factor within limits.
- Distributors are responsible for maintaining voltage harmonics, voltage levels and frequency within predefined tolerances.
Transition to a fully renewable grid
The modern grid is now comprised of many direct current (DC) devices from both a source and load perspective. Every time we convert between alternating current (AC) and DC, harmonics are introduced. This makes it especially important to keep a close eye on power quality.
When harmonics are introduced into the grid, there can be dips and peaks in voltage and power can be distorted. More than ever it is important to understand the quality of the power entering your installation, the only way to do this is through effective metering.
Save energy
By monitoring and analysing power quality parameters, organisations can identify opportunities to improve the efficiency of their electrical system and equipment performance.
If a business has multiple sites, it can use benchmarking to find anomalies and identify opportunities to improve energy performance and reduce operational costs.
Under NABERS, an organisation must commit to ongoing energy management through consistent monitoring with an auditable trail. It’s therefore essential to gather and analyse data.
Understand why power was compromised during a disruption
It’s very difficult to diagnose an electrical fault correctly without meter data as electricity is something we can’t see. If a piece of equipment has faulted, a circuit breaker has tripped or equipment has become damaged, there’s no way to identify the entry conditions without metering data. The fault itself can change conditions and make it difficult to understand the pre-existing condition and consequent result of a fault.
However data is not only important following a fault. By monitoring power quality over time and analysing data correctly, operations and facilities teams can gain insight into the glitches which may lead to bigger issues in the future. This allows them to take pre-emptive measures before a fault occurs.
Who’s going to analyse my metering data?
Our clients often tell us they don’t have the resources to implement, or understand, the full monitoring capability of their meter. Some software solutions and monitoring platforms allow alarms to be raised and can generate reports automatically. This can allow an operations team to engage with an expert when they need specialist support.
In the future, we see artificial intelligence (AI) having the potential to take high quality metering data, look at trends and identify issues before an outage occurs. We’re not there yet… but it’s only a matter of time before we can employ this resource to do the work we can’t find a team member to do.
With the increasing collection of data and ongoing advancement in AI, we’re seeing the first AI-enabled solutions entering the market which can assist in monitoring, analysing and predicting power usage on a range of inputs. This trend is anticipated to continue and accurate and reliable energy monitoring solutions will play a key role in this future.
What do you need your meter to analyse?
Before starting a building’s electrical design, clients and design teams need to have a strategy in place to understand what information needs to be monitored. An experienced electrical consultant can provide guidance on what should be analysed when they know the purpose of a building or facility. Their metering advice should then be based on functionality that helps the facility achieve its purpose.
While it can be easy to say we should have premium meters in all locations, every project has a budget and recognising where each device will provide the highest level of value is essential.
Meter design and specification
To begin with, an electrical engineer will review a facility’s requirements, making recommendations for improvements and providing a range of solutions. This sets the foundations to ensure a meter is properly specified and determine if there’s a sufficient monitoring platform to interrogate the data captured.
A multidisciplinary electrical team will also consult with other teams to identify the location of key equipment – for example fans, air conditioning units, chillers and pumps – which may generate poor power quality or fail prematurely due to increased load consumption.
Conversations with a smart buildings infrastructure team are also important to ensure the devices can be integrated. To make full use of information, it‘s important to ensure all the systems and platforms are talking to each other.
As a general rule, engineers normally specify a higher-end meter on the main incomer to identify transients or disturbances from the grid and a more basic meter on the outgoing supply and distribution boards. However specialist loads which present an increased risk need to be identified and may require additional monitoring.
It doesn’t end at selecting the right meter. There’s no point installing a premium device if all you are going to monitor is voltage, current, power and energy.
If a premium meter is being installed, organisations need to develop an effective strategy to extract data. This would include trending of harmonics, frequency, power factor, transients, undervoltage and overvoltage.
Meter installation and integration
High performing metering installation requires the coordination of many different teams:
- Electrical engineers specify the right products and information to be monitored.
- Electrical contractors ensure the proposed meters meet the brief before physically installing and commissioning.
- Project managers and quantity surveyors get involved early to ensure budgets are sufficient for required metering systems.
- All project teams are involved in ensuring successful integration of the meter into the electrical system. This includes:
- set up and configuration, including connecting a central monitoring platform
- testing and calibration
- data validation and verification – is what’s being picked up in the field correlating with what we’re seeing on the platform?
- integration with other systems, for example an energy management or other monitoring system
- building tuning period – this allows for establishing a baseline set of data and the opportunity to remedy any issues with set up and power quality. It also ensures users aren’t fatigued by false alerts.
- Electrical contractors, metering suppliers and integrators to train facilities managers and operations teams in how to use the meter and analyse data.
Don’t buy a Ferrari and only use it for the school run
The integration phase is where projects are most often compromised. In our experience, teams are eager to finish up when they’re nearing the end of a weighty building or infrastructure project. As a result, systems aren’t fully set up and data isn’t properly validated. Project teams have a misconceived idea that they’ll save money by closing their project promptly.
Unfortunately, the impact of incorrect configuration is that it costs significantly more over the long term. It jeopardises operational continuity, reputation and, depending on the facility’s purpose, lives.
We encourage capital works teams to consider the specification of any technology they’ve employed and work with their contracted consultants to fully realise its potential. After all, you wouldn’t buy a top-of-the-range Ferrari and only use it for a 5 km round trip to drop off the kids.