Steel is the dominant material in a lift. While around 40 per cent of all steel produced is through recycling, only about 60 per cent of steel is recycled.[1] Millions of tons go to landfill every year.
Steel production is also highly polluting. Wastewater from the coking process is highly toxic and contains a number of carcinogenic organic compounds as well as cyanide, sulphides, ammonium and ammonia.[2]
When upgrading a building, it’s remarkable how much can be modernised without needing to be replaced. Often, this gives you a better outcome for the building and its occupants.
Here’s what to consider as you embark on your building refurbishment.
1. Understand the anatomy of a lift
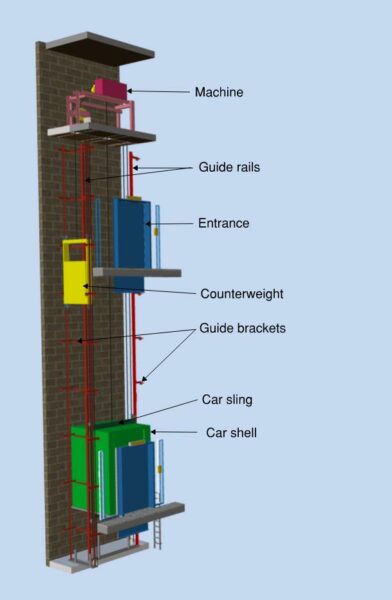
2. Develop the specification for your lifts
The first place to start is understanding your vertical transportation goals:
- Forecasted passenger numbers, now and into the future.
- Building grade and associated level of sophistication required.
- Passenger experience.
- Desired technology and smart buildings integration.
- Available space.
From here, you need to fully understand the infrastructure of your existing lift system:
- What type of lift system does the building currently have?
- Do the numbers of lifts and sizes of the existing lift system satisfy the forecasted performance requirements?
- Are the existing components in a condition that’s suitable for retention?
- Are there components that can be replaced or modernised?
- Does the lift system have the potential for technology integration?
A vertical transportation consultant can work with you to analyse these specifications and help you decide whether your existing lifts have what it takes to meet the needs of your planned building.
3. Understand the parts of a lift can you modernise and replace
While many things about lift manufacture have changed – size, sturdiness and weight, for example – the essential components remain the same. This makes it relatively easy to replace individual parts when modernising.
The parts of a lift which are most susceptible to wear and tear are those that move, rub or heat. These include:
- machines
- gearboxes
- car door operators
- landing door systems
- ropes
- electrical components such as switches, contactors, door locks.
All of the above components can be replaced as part of a modernisation. And, in doing so, the specification of replacement equipment can be optimised to ensure the improved performance and longevity of the completed system.
The decor of a lift can also appear tired and worn after a number of years. Individual parts can be removed and replaced and include:
- timber panelling
- colour-backed glass
- veneer
- stone and marble.
Much of the steel used doesn’t form part of any individual moving parts and therefore doesn’t wear as much as other parts. This makes it easy to retain. Steel parts include:
- guide rails
- machine beams
- brackets
- car slings and frames
- car shell (when made of stainless steel)
- wiring conduits and ducts.
Wear and obsolescence
Throughout the life of a lift, certain components will inevitably succumb to wear and tear. Others will fall foul to obsolescence or come up against compliance issues. Parts that can become worn or obsolete include machines and power units, door operators, controllers, push buttons and other electronic components. A vertical transportation specialist can advise on the parts that need upgrading.
4. Unpack the pros and cons of modernisation
It’s not surprising that building owners can be wary of choosing to modernise over the perceived safety of full replacement. As vertical transportation consultants, we look to engage with building owners, architects and scheme designers at an early stage to determine their particular requirements and establish the most effective solution for their building. As a part of that process, a consultant can explain the benefits and drawbacks of the options available.
Embodied carbon
The importance of sustainability in building services has never been more evident. The industry is rapidly responding to an ever-growing demand for smarter, greener design as we strive to reduce our carbon emissions.
While the focus has traditionally been on energy efficiency, there’s an increasing awareness of embodied carbon in the design and construction process. This is leading to a cradle-to-cradle approach in building design, with a greater emphasis on refurbishment and reuse over replacement.
In an average 6-storey building, with 11,000 m² net lettable area, a lift system can account for around 3.5 to 4 per cent of the building’s total whole-of-life embodied carbon. This is equivalent to the total embodied carbon of raised access floors.
A typical new lift, rated to carry a load of 1,600 kg, travelling 6 stops weighs around 8,750 kg. Over 90 per cent of the lift is made of steel. That’s over 24,150 kg of CO2 per lift.[3] A building like this could have 4 or 5 lifts, bringing the total to over 110,000 kg of CO2. And, this is all before considering the additional impact of transport and installation.[4]
Up to 6,000 kg of this steel could be retained and reused, per lift, as part of a modernisation, saving 16,500 kg of CO2 and significantly reducing the amount of embodied carbon within the building.
We’ve compared the embodied carbon of installing new lifts and refurbishing existing lifts.
Single new lift, 1,600 kg load rated, travelling 6 stops
Project type / Material breakdown | New installation | Modernisation |
---|---|---|
Weight of ferrous metals | 8,750 kg | 8,750 kg |
Metals reused | 0 kg | 6,000 kg |
CO2 | 24,150 kg
(3.5 to 4% of building’s carbon, equivalent to the pipework and chilled beams combined) |
7,590 kg
(59% carbon saving) |
Demonstrating a carbon saving means nothing if the project stakeholders cannot be convinced of the ability to successfully refurbish the lift to the standard of a new lift. Here are the further benefits that refurbishment can offer.
Functionality
Modernisation allows for the replacement of machines or power units, controllers and electronics and, potentially, doors and door operators. It also provides the opportunity to:
- improve speeds, depending upon available pit and headroom space
- increase entrance widths (requiring building works)
- upgrade call handling by replacing existing conventional call systems with destination control
- introduce new technologies such as monitoring systems, in-car infotainment and the Internet of Things
- reduce energy consumption by fitting more efficient machines and drives, LED lighting and energy saving control systems
- lower the level of embodied carbon within the building by retaining serviceable components from the existing lift.
Operational disruption
A replacement lift requires intensive building work which is noisy, disruptive and has a high carbon outlay.
Replacement lifts require noisy structural building work to accommodate different structural load profiles and shaft ventilation. Structural entrance openings, pockets for new steelwork and scaffolding may also be needed.
Modernisation can provide additional benefits in an occupied building where noise, dust and dirt can seriously inconvenience occupants and business activity. It’s unlikely to require changes to the structural core of a building, minimising disruptions caused by building works.
No major lift project can remain invisible. However, with much of the heavy equipment being retained, modernisations tend to cause fewer interruptions to building operations.
Energy efficiency and reduced maintenance
The majority of energy efficiency features considered by sustainability rating tools are available in a lift modernisation. These include LED lighting, reduced power modes during quiet periods, low standby current, variable frequency (VF) and regenerative drive systems. Supercapacitor energy storage devices can further improve efficiency on intensive-use lifts.
Ageing hydraulic lift systems have traditionally been replaced with machine room-less lifts (MRLs) for improved efficiency. However, even hydraulic lifts are now benefiting from new VF with electronic valve technology and plant-based oil. This makes modernisation a more attractive option.
Capital cost
But, what are the financial implications of retaining and refurbishing versus ripping out and replacing?
Lifts that are mass produced (sometimes known as package lifts) can be cheaper in the short term. However, most are unlikely to be suitable for modernisation which introduces a replacement cycle of 15-year intervals. With the right investment in quality value-engineered equipment at the time of an initial modernisation, the cost of a refurbished lift can be equal to a new lift, allowing future modernisations to be completed at 20-year intervals. This offers lifetime cost-saving benefits.
And, of course, the added benefits of a refurbished lift include reduced carbon emissions and environmental impact.
5. Improve the longevity of your lift
What’s in your lift well?
The old saying ‘They don’t build them like they used to’ is somewhat of a cliche, but, when it comes to vertical transportation, there’s a lot of truth in it. Older equipment was typically engineered to last. The guides, car frame and counterweight steelwork from 1960s, 70s and 80s were often more heavily engineered than those often found in today’s systems and can have up to 40 more years of life in them.
More recent lifts, while perhaps not containing as much steel in their design, will also lend themselves to modernisation. It’s worth carrying out a detailed condition survey on any existing equipment before deciding on its future.
New parts for an old lift can make it as good as new and, sometimes, even stronger. They can also improve the user experience, energy efficiency, passenger capacity and life expectancy.
The Chartered Institute of Building Services Engineers (CIBSE) suggests the life of some light-duty machine room-less lifts can be as low as 10 years with little viability for future upgrades. Other sources recommend designing for a lifetime of only 15 years for a typical modern office building lift. Conversely, a high quality electric traction lift can provide up to 25 years of service with the potential for upgrades.
CIBSE, and other advisory bodies, provide these recommendations as guidelines which make allowances for some modern day mass-engineered lifts which are made of lighter materials and have a shorter lifespan. Steelwork from a well-engineered lift of the 1960s was built to last much longer than these guidelines. A lift will still be compliant if this lifetime is extended through compatible replacement parts.
Non-compliance is rare when it comes to lift steelwork. In most cases, there’s little chance of those parts falling out of compliance with any current standards.
Increased efficiency can lead to reduced maintenance and longer lifespan. When not in use, your lift will go into stand-by mode. This significantly reduces energy consumption and reduces the demand on the individual parts which, in turn, decreases the need for maintenance and extends lifespan.
6. Learn from buildings that have done it well
We’re currently working with The University of Queensland (UQ) to improve the lifts throughout their campuses. They asked us to improve reliability and availability, reduce maintenance and strengthen infrastructure and technology for the future.
Our vertical transportation team started with an audit to determine the age and condition of the lift systems, type of technology installed, level of code and Disability Discrimination Act (DDA) compliance. We also highlighted areas of non-compliance with UQ design standards including minimum car dimensions. Our recommendations included upgrade options covering complete replacement, modernisation and modernisation with re-orientated car and counterweight.
We estimate the 9 buildings where we’ve been able to modernise existing lifts, rather than replace the lift system, will save UQ 54,000 kg of steel, the equivalent of 150,000 kg of CO2. This will make a huge impact in helping UQ achieve its mission of ‘delivering for the public good’ and ‘purposefully investing in infrastructure [and] systems‘.
Completed works:
- Retained traction lift and modernised: Foxtail Building, Ritchie Research
- Retained hydraulic lift and modernised: Biological Sciences, JKMRC Building, Banksia Building, Zelman Cowan
- Replacement of existing lift with machine room-less lifts: Public Health Building.
In construction:
- Modernisation with re-orientated car and counterweight: Skerman building, Social Sciences Building, Axon Building
- Replacement of existing lift with machine room-less lifts: Forgan Smith Tower, Steele Building (lift 14), Richards Building (lift 15).
7. Put yourself in the shoes of someone going up… and down
During building refurbishments, upgrades and modernisations, we too often see lifts being ripped out when they’re good enough to keep. As business priorities shift towards decarbonisation and net zero, lift reuse is becoming a practical and beneficial option to ripping out and replacing. By reducing the lift system’s embodied carbon, it can free up a project to channel its carbon budget on things that enhance user experience, for example better air quality or on-site amenities.
We understand the obstacles many businesses face when it comes to modernising a lift – building for high performance, increased capacity, future-proofed infrastructure, maximum net lettable space and stakeholder agreement. These outcomes can all be achieved with a vertical transportation strategy that prioritises the planet as well as project goals and passenger experience.
[1] https://www.theworldcounts.com/challenges/planet-earth/mining/advantages-of-recycling-steel
[2] https://www.theworldcounts.com/challenges/planet-earth/mining/environmental-impact-of-steel-production
[3] The carbon factor in this calculation is 2.76 – a generic OneClick LCA value. It assumes that 20 per cent of the content in the steel is recycled (based in UK production).
[4] We’ve based this embodied carbon on data taken from an environmental product declaration from a lift manufacturer. This is an approximate estimation used to illustrate how much carbon steel contains.