Owners Beltane Asset Management and Angelo Gordon (AG Beltane) were quick to recognise the wasted opportunities of One Millennium Bridge (formerly known as Millennium Bridge House) and tasked our mechanical engineering team with freeing up space to house a unique rooftop restaurant, office accommodation and expansive terraces.
As well as maximising the net lettable area by creating space for additional facilities, we found solutions that would reduce operating costs, expediate AG Beltane’s journey to net zero carbon and improve the wellbeing of occupants – all critical considerations for a landlord in today’s climate.
Increasing revenue by making every square foot work hard
AG Beltane had a vision for One Millenium Bridge. It had to be a sustainable, next-generation riverside workspace, with spectacular terraces and outstanding on-site amenities. Okay, we thought, that’s going to need some creative engineering!
Rooftop real estate in London comes at a premium so it was imperative to move the building’s plant and boilers to a less valuable location. (The rooftop and upper floors tend to have a higher rental value than lower floors because of the views, rooftop terrace and penthouse potential.)
Here’s what we discovered:
- The plant, in its existing specification, couldn’t be moved to a different location. There was nowhere else in the building that could accommodate such large machinery – it filled most of the occupiable part of the existing roof.
- It couldn’t be condensed and made taller due to height restrictions imposed by the St Pauls Heights policy. Also, it couldn’t be moved to the basement or ground floor because of the busy dual carriageway that runs under the building (Upper Thames Street).
- Any solution needed to enable the building’s waste heat to be rejected without the need for a large heat rejection plant. (This is the heat generated by users, equipment, lighting and more.)
The solution took some exploring, testing, developing and refining, but in the end it was simple. Thermal storage – a technology more commonly used in the industrial sector – could be applied to a commercial office building. Thermal storage enables daily peak cooling or heating loads to be spread out over a 24-hour period. This enables the building’s needs to be satisfied with smaller plant that runs over a longer period of time.
However, this only solved half the problem. The building had large gas-fired boilers on the roof to produce heating and hot water. As part of the client’s sustainability brief was not to have any combustable fuel on site, an alternative solution was required. We initially proposed the thermal storage technology, to reduce the peak heating load, but this time it was linked to air source heat pumps.
This ‘all electric’ solution would help improve local air quality and edge London along on its journey towards net zero.
Finally, as we explored possibilities for making best use of the waste heat, we realised that water source heat pumps could transfer the rejected heat from the cooling plant into the low temperature hot water store. This recycling of heat would save huge amounts of operational energy.
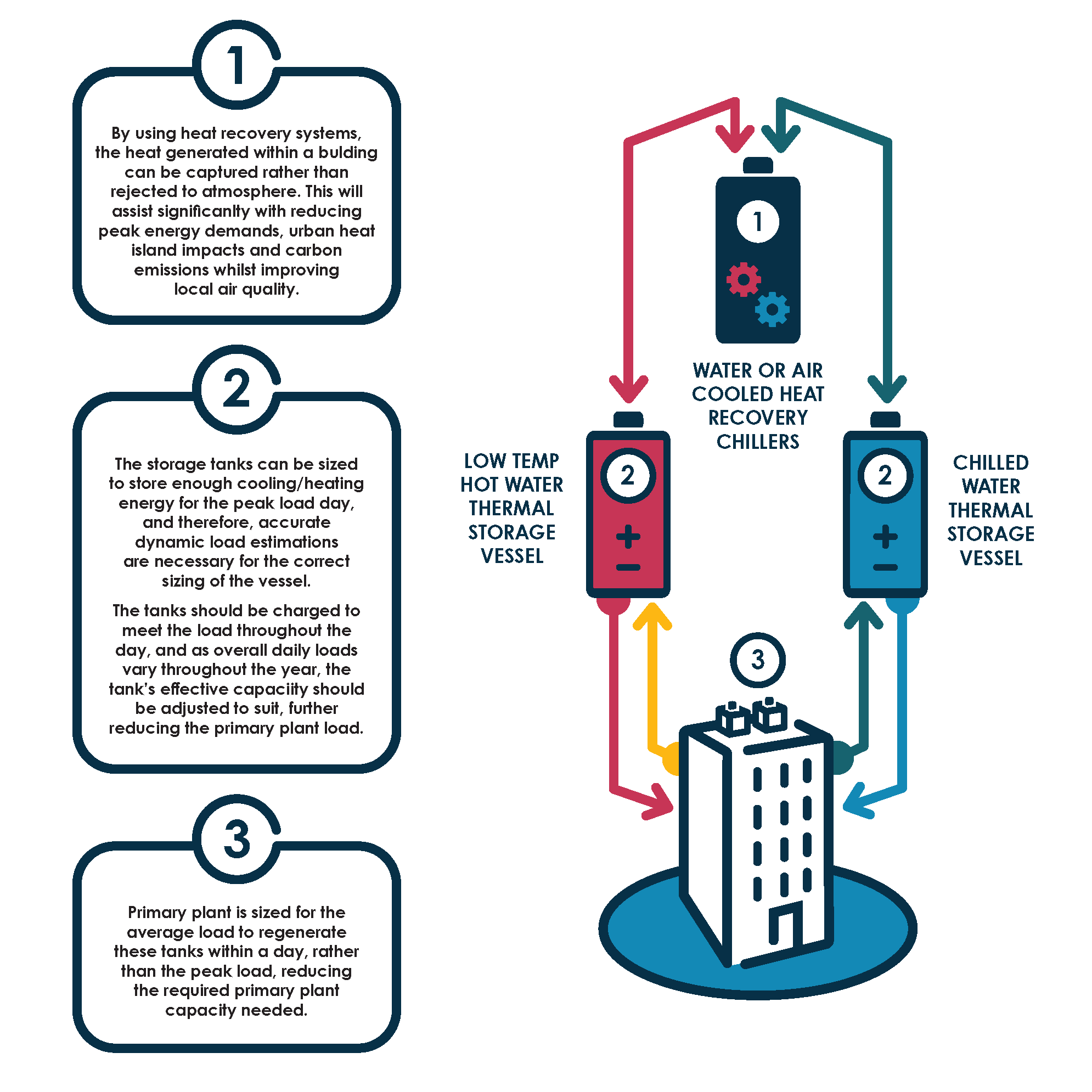
Improving system resilience for critical services
A major reason heating and cooling systems with thermal storage are deployed in the industrial sector is their ability to keep going if something should fail. Heating and cooling are no longer on-demand, instead they’re backed up and available when required. By applying this solution to a commercial environment, we were able to reduce the risk of the building and its facilities underdelivering for tenants and visitors.
Reducing operating costs by putting sustainability first
Our mechanical engineering team was able to develop significant cost savings through:
- high-efficiency mechanical ventilation with heat recovery
- high-efficiency water cooled chillers, low temperature hot water storage and chilled water storage – all of which enable the recovery of waste heat to produce ‘free’ heating
- reduction of peak loads and energy consumption for heating and cooling
- 100% electric solution, with no gas on-site for heating or cooling.
The building will achieve BREEAM Excellent certification, EPC A and WiredScore Platinum – challenging ratings to achieve when refurbishing a building. The technology that underpins the building’s core services has been fundamental to achieving the necessary energy performance as well as unlocking enhanced wellbeing and biodiversity.
Maximising the health and wellbeing of occupants
The benefits of an expansive rooftop terrace reach far beyond the view and revenue potential. Evidence shows that when the outdoors is integrated into our working day we can feel better, more energised and experience enhanced cognition. We can also become more open in our communication and have better conversations.
The mechanical engineering solutions we developed freed up 29,000 ft² of outdoor space, 23,500 ft² from the rooftop alone. The green roof, on level 6, provides private office gardens, a public space and rooftop restaurant. Terraces on level 5 are also landscaped and planting is included at the balconies on levels 3 and 4. In addition, there are two sunken courtyard gardens on level 5 which have access to the private garden on level 6.
Close collaboration with our electrical engineering team, the architect (Piercy & Co), structural engineer (Heyne Tillett Steel) and wider design team also facilitated ventilation, air conditioning and daylight strategies which maximise comfort for the occupants of the building. These include:
- ventilation that minimises the concentration and recirculation of air pollutants, reducing the risk of poor air quality
- fresh air from the windows overlooking the River Thames (the natural clean corridor along the river)
- reduced risk of summertime overheating
- design which improves average daylight provision by 15% when compared to daylight levels before refurbishment.
Futureproofing the City of London for the next generation
The ideas and solutions for this next-generation workplace have come from NDY’s mechanical and electrical engineering consultants, AG Beltane’s project team, Piercy & Company architects and Heyne Tillett Steel.
It’s through our combined curiosity and creativity that we’ve landed on these exceptional results. We’re never afraid to challenge assumptions, remove anticipated outcomes and create better solutions.
Our very best mechanical minds are those that think laterally, use their knowledge in innovative and unusual ways and ask each other – what if? It’s these minds that are forging a sustainable path for buildings in London, across the United Kingdom and around the world.